Factory Cheap Hot Gas Flame Cutting Torch - Reaction bonded silicon carbide Sagger – ZhongPeng
Factory Cheap Hot Gas Flame Cutting Torch - Reaction bonded silicon carbide Sagger – ZhongPeng Detail:
The product is ideal for industrial kiln, sintering, smelting and applicable to all kinds of products. In the field of chemical industry, petroleum and environmental protection with a wide range of applications.
1) Heat shock stablity
2) chemical corrosion-resistant
3) High temper-endure(up to 1650°
4) Wearing/corrosion/oxidation resistant
5) Highly performance of mechanical strength
6) Cleaning or etching the hardest sub-surfaces
7) Used for grinding, lapping, and wire saw cutting as well as abrasive blasting
Description:
A crucible is a ceramic pot use to hold metal for melting in a furnace. This is a high quality, industrial grade crucible used by the commercial foundry industry.
What It Does:
A crucible is needed to withstand the extreme temperatures encountered in melting metals. The crucible material must have a much higher melting point than that of the metal being melted and it must have good strength even when white hot.
It is possible to use a home made steel crucible to melt metals such as zinc and aluminum, because these metals melt at a temperature well below that of steel. However scaling (flaking) of a steel crucible interior surface is a problem. This scale can contaminate the melt and thin the crucible walls rather quickly. Steel crucibles will work if you are just getting started and don’t mind dealing with the scaling.
Common refractory materials used in crucible construction are clay-graphite, and carbon bonded silicon-carbide. These materials can withstand the highest temperatures in typical foundry work. Silicon carbide has the added advantage of being a very durable material.
Our Clay Graphite Bilge Shape crucibles are rated for 2750 °F (1510 °C). They will handle zinc, aluminum, brass / bronze, silver and gold alloys. The manufacturer states they can be used for cast iron. Made in the United States!
Crucible Shapes:
A bilge shaped (“B” Shape) crucible is shaped like a wine barrel. The “bilge” dimension is the diameter of the crucible at its widest point. If there is no bilge diameter shown then the top diameter is the maximum width.
A rule of thumb states that the # of a “bilge” crucible gives its approximate working capacity in pounds of aluminum. For brass or bronze use 3 times the crucible #. For example a #10 crucible would hold approximately 10 pounds of aluminum and 30 pounds of brass.
Our “B” shape crucibles are typically used by hobbiests and frequent casters. These are a high quality, long lasting commercial grade crucible.
Check the tables below to find the right size for your job.
How To Use It:
All crucibles should be handled with properly fitting tongs (lifting tool). Improper tongs can cause damage or complete failure of a crucible at the worst possible time.
A disk of cardboard can be placed between the crucible and the furnace base prior to heating. This will burn off, leaving a layer of carbon in between and prevent the crucible from sticking to the furnace bottom. A coating of Plumbago (Carbon Black) does the same thing.
It is best to use a different crucible for each type of metal to avoid contamination. Also be sure to completely empty the crucible after use. Metal left to solidify in a crucible can expand on re-heating and destroy it.
Please temper new crucibles or those that have been in storage. Heat the empty crucible for 2 hours at 220 F (104 C). (Use adequate ventilation. New crucibles will smoke as the glaze sets.) Then fire the empty crucible to a red heat. Allow the crucible to cool to room temperature in the furnace before use. This procedure should be followed for ALL new crucibles and for any crucible that may have been exposed to damp conditions in storage.
Store all crucibles in a dry area. Moisture can cause a crucible to crack on heating. If it has been in storage for a while it is best to repeat the tempering.
Silicon carbide crucibles are the least likely type to absorb water in storage and typically don’t need to be tempered before use. It is a good idea to fire a new crucible to a red heat prior to its first use to drive off and harden factory coatings and binders.
The material should be placed into the crucible VERY loosely. NEVER “pack” a crucible, as the material will expand on heating and can crack the ceramic. Once this material has melted into a “heel”, carefully load more material into the puddle for melting. (WARNING: If ANY moisture is present on the new material a steam EXPLOSION will occur). Once again, don’t tightly pack in the metal. Keep feeding the material into the melt until the required quantity has been melted.
WARNING!!!: Crucibles are dangerous. Melting metal in a crucible is dangerous. Pouring metal into molds is dangerous. A crucible may fail without warning. Crucibles can contain hidden defects in materials and manufacturing which can lead to failure, property damage, personal injury, injury to bystanders and loss of life.
Crucible Base Block
Description:
BCS A base block is a high temperature pedestal used to raise up a crucible to the heat zone of a furnace.
What It Does:
A base block is generally used in a gas fired foundry furnace to lift the crucible up so that the burner flame doesn’t directly blast into the thin wall of a crucible. If the burner flame is allowed to directly strike the crucible it can cause errosion of the wall of the crucible thus shorting its life. The proper way to prevent this is to use the base block to raise up the crucible out of the burner zone.
Raising the crucible also allows it to be in the “heat zone” of the furnace. Although the burner flame enters the body of the furnace at the bottom the hottest zone is from the middle up to the top. It is in this region that the walls of the furnace are heated by the circulating gas most effectively. Having the sides of the crucible in this region promotes the best heating from the turbulent gas stream and by the heat radiation of the glowing furnace inner walls.
How To Use It:
The base block should be tall enough to have the burner flame aligned with the top of the block. It’s ok if the top of the block is higher than the burner inlet as well. What you don’t want is to have the flame hitting the thinner sides of the crucible. It is also acceptable if the flame strikes the thicker bottom portion of the crucible as this part is not as suseptible to wear from the gas.
Product detail pictures:
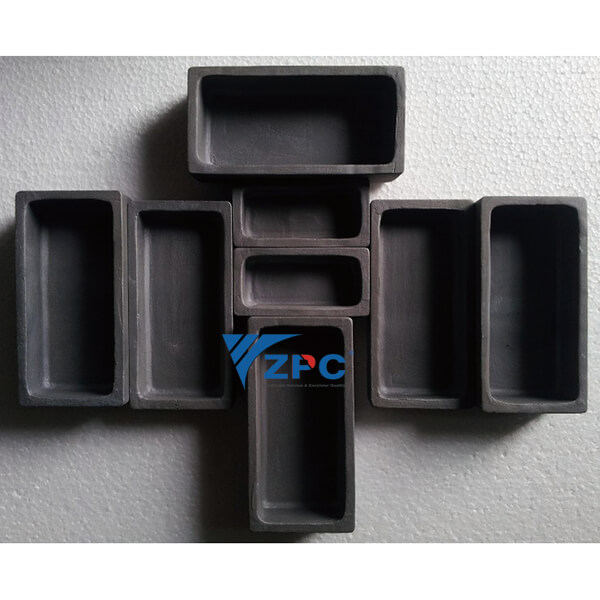
Related Product Guide:
Wear resistance block, plates and inner lining
Wear resistance SiC ceramic inner lining
Factory Cheap Hot Gas Flame Cutting Torch - Reaction bonded silicon carbide Sagger – ZhongPeng, The product will supply to all over the world, such as: , , ,
Shandong Zhongpeng Special Ceramics Co., Ltd is one of the largest silicon carbide ceramic new material solutions in China. SiC technical ceramic: Moh’s hardness is 9 (New Moh’s hardness is 13), with excellent resistance to erosion and corrosion, excellent abrasion – resistance and anti-oxidation. SiC product’s service life is 4 to 5 times longer than 92% alumina material. The MOR of RBSiC is 5 to 7 times that of SNBSC, it can be used for more complex shapes. The quotation process is quick, the delivery is as promised and the quality is second to none. We always persist in challenging our goals and give our hearts back to society.

